Scroll down
How Can Industrial Companies Reduce Warehouse Overhead?
It is a must and an urgent need for businesses, particularly for the logistics and distribution executives, to reduce cost and maintain it at optimum and acceptable levels.
But like any other business component or division, maintaining and managing a warehouse facility incurs considerable cost. The cost here covers many aspects including overhead and operational cost; costs incurred due to spoilage, damage or customer rejections; and delivery and distribution costs.
And like any business division, inefficient operations and execution will incur even more costs that could be detrimental to the profitability and sustainability of the business. On top of that, an inefficient logistics and warehousing system will tie up valuable capital through non-moving inventory. Previous studies show that in the US alone, as much as $1.1 trillion in capitalization is tied up with non-moving inventory.
So, it is a must and an urgent need for businesses, particularly for the logistics and distribution executives, to reduce cost and maintain it at optimum and acceptable levels. In this regard, the following discussion shall focus on reducing “overhead” without causing any adverse effect on warehouse operations and productivity.
But before that, let us first identify the factors that affect overhead costs from a warehouse perspective.
Factors Affecting Overhead Costs
In the field of warehouse management, benchmarked companies like Dell and Toyota are considered among the top companies with the most efficient and reliable supply chain management systems. These companies have streamlined their operations so well that they only spend more than 50% less on their supply chains compared to other companies performing on the average.
This goes to show how important a reliable and efficient warehouse system can affect logistics costs. Aside from warehouse efficiency, other factors can also affect overhead costs. What is important here is to gain a better understanding of these factors, so you can have a better and more effective plan of action to reduce overhead costs.
Decrease in Productivity
Inefficiency in warehouse operations will create a big impact on productivity. The decrease in productivity, however, can be attributed to several reasons, ranging from unproductive or inefficient workers, or inefficient workflows and systems that result in bottlenecks and delays.
For example, it would be surprising to know that as much as 46% of Small and Medium businesses still make use of manual systems while some do not even have an inventory tracking system in place. It would be no wonder why such methodologies would result in a decrease in productivity.
Unexpected Increase in Product Demand
Many businesses engage in volatile markets where the increase in product demand may come unexpectedly. During such events of sudden spikes in the demand, warehouses and logistics centers have no course but to resort to drastic measures to cope up with the sudden demand. In many cases, such adjustments to ensure delivery on time would entail premium shipping charges, which of course would mean higher costs than usual.
To cope with such sudden increases in demand, companies resort to stockpiling multiple SKUs in their inventory or expanding the number of items they have on-site. It would be to their advantage if this added inventory can meet the sudden increase in demand, but it also creates the risk of unsold inventories should there be sudden turnarounds in these demand increases as well.

Unexpected Increase in Product Demand
Unexpected Increase in Product Costs
Sudden increases in product costs is also another factor that affects overhead costs. Price changes that are not monitored can come unexpectedly, putting the business and warehouse in a difficult situation to adjust and shoulder the increase in costs.
Unexpected Increase in Shipping Expenses
Shipping expenses are another big factor that can affect the overall overhead costs. If not managed properly or if shifts and changes in costs occur without the business knowing about it due to lack of monitors. While changes and adjustments to shipping costs may not be necessarily high in itself, these costs if factored in collectively can add up quite severely, resulting in additional costs incurred.
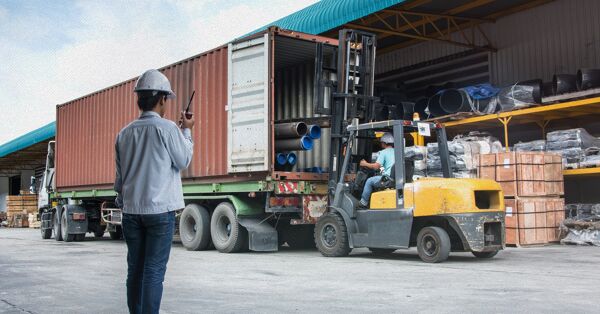
Unexpected Increase in Shipping Expenses
Specific Actions to Reduce Warehouse Overhead
Now that the factors affecting overhead costs are identified, it would be high time to move forward and implement the following actionable steps to reduce overhead warehouse costs:
Optimize Storage Space
The size of warehouses has increased tremendously since a decade ago, requiring as much as a third more space than what was the standard before. Back in the early 2000s, average warehouse sizes range at 127,000 sq. ft. level. This figure has now increased to 180,000 sq. feet at the average.
This requirement is attributed to changing demands by the market, wanting more product choices and varieties, resulting in multiple SKUs being maintained by warehouses. As technology continuously improves and creation of products much more efficient, even more product choices will come out in the market – requiring even more storage space.
To address such scenarios, warehouses should focus on implementing systems and technologies that not only provide them solutions for optimizing storage space but also on how they manage and handle the flow of materials in these spaces. These include the use of optimized layouts, bins, and shelves, coupled with the use of new technologies like RFIDs, Internet of Things (IoT) and Electronic Shelf Labels (ESL).

Optimize Storage Space
Protect and Safeguard Your Inventory
It may come as a surprise, but businesses with inefficient warehouse systems are incurring losses amounting to hundreds of millions or even billions of dollars. Such losses are attributed to damages to stock items, misplacement of items during handling and delivery, and theft. On top of that, such damages, slow delivery, or failure in delivery will create an irreparable strain in the business-customer relationship.
There are now several improvements in rack, bins and shelving systems that are geared towards providing more robust physical protection to goods and items while within the warehouse facilities and also during transport. These can be integrated with security systems such as RFID, IoT-enabled security cameras, geolocation and geofencing, and the several varieties of ESL products.

Protect and Safeguard Your Inventory Using ESL
Implement Efficient Forecasting System
The number of SKUs being handled in an average warehouse continuously increase by as much as 18.5%. Such proliferation of SKUs is due to several factors, ranging from increasing demands of the market or technological trends that drive consumer demand.
Such increases in SKUs and inventories can make the forecasting and maintenance of the warehouse system much more complicated, particularly if such is done manually. A good Warehouse Management Software with analytics components can give you a better insight into the behavior and flow of products, giving your planning group better references where they can base their forecast numbers.

Implement Efficient Forecasting System
Leverage on Cross Docking Systems
Shipping costs are some of the most considerable costs in warehouse and logistics operations. Such costs increase quite significantly depending on your scale and area of operation. The more destinations you have, the higher the shipping costs.
To address this, it would be good to take a look at Cross Docking, which is basically to cut out the middleman in the delivery process. This involves quick transfers to customer delivery vessels directly from suppliers. These systems save time, storage space, labor costs, and shipping fees.
Implement Energy Cost Reduction Initiatives
The larger a warehouse is, the more power and energy it consumes, and this entails costs. This includes energy for machinery, lighting, and cooling systems. In the United States alone, lighting and cooling account for up to 75% of the annual energy consumption used in warehouses.
There are several energy efficiency systems that you can implement in your warehouse. Lighting can be optimized by using a combination of natural lighting and highly-efficient LED lamps. Insulation, high-performance filters, and cooling systems can improve your HVAC requirements as well.
Optimize Labor-Related Costs
Labor costs are the largest factor that affects overhead costs. As much as 65% of a warehouse’s budget is allocated to labor. Such labor costs balloon up due to manual and inefficient systems that take on more time resources from labor but produce fewer results.
For example, product picking takes up more labor time because of the amount of walking around isles and shelves, looking for particular items and goods. Bin systems that are integrated with innovative solutions like the Electronic Shelf Systems from SOLUM, RFID scanning systems, and other automation systems can improve employee efficiency and reduce costs.

Optimize Labor-Related Costs
Leverage on the Power of Technology
Manual and inefficient systems should be a thing of the past. Unless you implement and leverage new technologies to improve your warehouse system, you will be in no position to reduce and optimize your overhead costs. There are several such technologies available in the market now, and it's up to you to fully implement such systems.
The use of an efficient Warehouse Management System (WMS) integrated with innovative technologies like scanners and RFIDs is something businesses should look into. One example is the use of barcodes for medication, reducing administrative errors by as much as 41.4%. The use of wearable voice command devices is proven to increase warehouse efficiency by as much as 30 percent.
The use of mobile devices is something that up to 67% of warehouse managers are planning to implement to optimize their operations. This would be a far cry from the inefficient manual system for monitoring inventories, product picking, and other warehouse-related activities. Implementing a more automated and more integrated system for your inventory can increase overall warehouse productivity by as much as 25%.

Electronic Shelf Labels
The Take Away
Businesses need warehouses, and this is even made truer for companies that engage in the manufacture, sales, and distribution of physical goods and products. However, maintaining and operating a warehouse would incur costs, and such costs tend to balloon and increase when inefficient and manual systems are used.
There are many ways to cut warehouse expenses, particularly in overhead costs. The main thing to remember here is to implement systems that are geared towards increasing employee efficiency, streamline processes, optimize workflows and reduce losses due to wastages, misplacement, and theft.
Contact us today to know how we can help your warehouse reduce overhead.