Scroll down
How Do Electronic Shelf Labels Improve Order Picking?
One of the biggest cost contributors related to warehouse labor efficiency is order picking, contributing up to 36% of the overall labor costs.
This inefficient logistics and warehousing system will create a negative impact on the bottom line. One is non-moving inventory, which in worst-case scenarios would impede the proper flow and utilization of capital. Another one would be ballooning labor costs, which be substantial considering the 70% of warehouse costs are mostly attributed to labor. When summed up, such inefficiencies, revenue losses and incurred costs with make businesses lose millions or even billions of dollars each year.
One of the biggest cost contributors related to warehouse labor efficiency is order picking, contributing up to 36% of the overall labor costs. There are several factors that affect the productivity of the order picking process, and this is mostly related to how efficient the warehouse operation, workflows, and systems are. For example, up to 50% of order pickers' total work-hours are expended just by walking around the warehouse to search and process inventories.
The following provides best practice scenarios as well as recommendations for warehouse administrators on how they can improve the productivity of the order picking process. This list is not exhaustive, nor is this fully authoritative, but it would provide a good starting point to finally gain headway in warehouse efficiency and productivity.
Best Practices and Recommendations to Improve Order Picking Productivity
1. Go Paperless
In a highly technological and connected world, many still opt to use manual systems and used paper-based workflows in their warehouse operations. One big example is the use of paper-based pick which, is not only very tedious but is also highly risky and prone to errors. The simple fact of having to go to an office to have pick lists printed is already very cumbersome. Not only that, there is a big chance that the personnel will print the wrong list and go on spending a whole day picking inventories from a previous or totally wrong order.
Another paper-based element in manually-driven warehouses is the sticker labels used for racks, bins, assets, and items. The printing and sticking process are cumbersome and highly manual. There is a big chance for committing errors. The information in these labels is not automatically updated as well, creating the possibility that what is being used in the warehouse floor is not current or erroneous.
There are new and very innovative technologies that are primarily intended to usher in a paperless warehouse. These technologies include the use of RFID, the Internet of Things (IoT), Electronic Shelf Labels (ESL), mobile gadgets, and a host of other tools and equipment. Generally, the effectiveness of these tools is attributed to their integration and connectivity to a central Warehouse Management System, allowing managers and staff to work on real-time and highly accurate information. Warehouses who have already chosen this path have realized as much as 25% increase in their productivity.

Electronic Shelf Label
2. Choose the Right Order Picking Strategy that Delivers the Best Results
As mentioned earlier, travel time eats up half of an order picker’s total daily working hours, resulting in poor productivity and highly inefficient results. To increase productivity, it is imperative to reduce this travel time or create more output using the same picking hours. To achieve this, the warehouse should make use of the right order picking strategy that will deliver the best results in their own particular scenario.
Batch Picking Strategy
The basic idea for Batch Picking is to have the order picker pick and process multiple orders which involve the same SKU, all at the same time. This will minimize the number of times he would have to return to the same SKU location to pick inventories from several orders.
Zone Picking Strategy
This strategy is also often called Pick-and-Pass Order Picking. In this method, an order picker is required to pick multiple SKUs from within one particular zone based on multiple orders that he is assigned to. Once all the required SKUs from one zone is completed based on his order list, he then moves on to the next pick zone, until all orders are completed.
Cluster Picking Strategy
The key to an effective cluster picking strategy is to make use of multiple containers, usually a multi-tray trolley. In this strategy, an order picker will process multiple orders in one trip, assigning a different container for each order. He will then fill up each container according to the required SKUs as he passes through each picking section.
Wave Picking Strategy
This strategy required order pickers to process orders and fill them up with the required SKU one at a time. To make this effective, each order is properly coordinated according to an optimized schedule, thus maximizing the time allocated by the order picker for each run.
One strategy may not work for all business types as there is certain uniqueness in the delivery and order process depending on the nature of products or items being delivered. For many warehouses, a combination of these strategies would work better and deliver better results. On top of that, these strategies will be optimized further when used in combination with other recommendations here such as the use of technologies and automation systems.
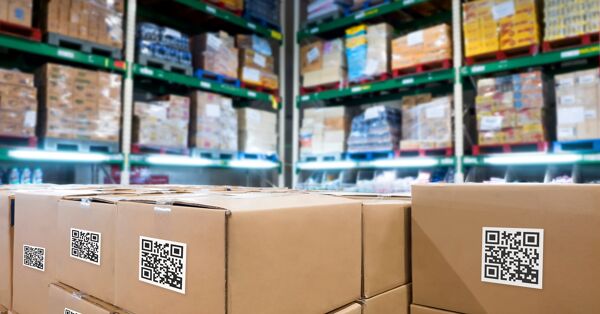
Inventory
3. Each SKU Should be Assigned with a Discrete Pick Location
The advancements in manufacturing technologies resulted in more product variations coming from the same brand or company. This is also driven by a growing and more dynamic consumer demand. Because of this, the number of SKUs that a particular warehouse handles has increased significantly. With multiple SKUs being handled, it is imperative that each SKU is assigned with a discrete pick location, otherwise, the warehouse will devolve into chaos.
The usual practice of putting multiple SKUs in a single bin location does not work and will only result in poor productivity. Having to search through multiple items to look for the specific SKU he needs will slow down the processing time the order picker needs to expend to complete the order. It will also be best to put fast-moving SKUs in special “hot zones” which have wider operating spaces will facilitate faster order picking and avoid congestion. Another strategy is to put the fast-moving SKUs at ground level, particularly when the warehouse layout is configured to allow vertical shelving. This makes it easy for the order pickers to access these SKUs by moving horizontally at ground level.

A Worker Picking in the Warehouse
4. Leverage on the Use of Innovative Picking Technologies
The tremendous advancements in technologies have simplified and optimized the way products are produced and services executed and delivered. This trend holds true for most, if not all vertical industries and is also apparent in the warehousing sector. These technologies include innovative tools, gadgets, software, and types of machinery that increases effectiveness, minimize manual handling, reduce the occurrence of errors, and increase productivity. Some of these innovative picking technologies are discussed below:
The use of scanners to verify every item for shelving or picking is a must if you want to eliminate such errors. With a scanner, even if two adjacent items have SKUs that look very similar, you can still pick the right one through scanning.
RF Handheld Scanners
Scanners make use of the traditional barcode system, which many stores and warehouses are quite familiar with, or they move up to a more advanced scanning system such as the use of RFIDs. The effectiveness of such scanning system relies heavily on the use of centralized software systems and wireless connectivity. A mobile and handheld scanning system make it easier and faster for order pickers to process orders using up to date information sent directly into the gadgets in their hands.
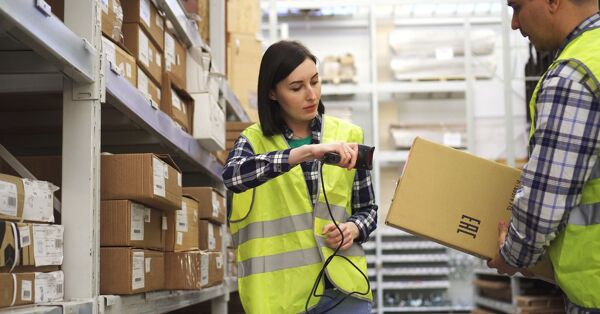
Worker Using an Advanced Scanning System
Pick-by-Light
This innovative system is growing in popularity and is known and proven to improve the efficiency of the picking process, and thus result in greater productivity. The system is easy to use and implement but will require the use of a centralized software that is integrated into the Warehouse Management System. The system then connects to an indicator light installed on the shelves or racks, or to the digital display and indicator LED of various Electronic Shelf Label configurations.

Electronic Shelf Labels for Pick to Light
With this system, the order picker can easily locate the SKUs needed for a particular order, acknowledge the pick through a simple button or interactive display, and order and inventory data is updated to the system. Specialized Pick-by-Light devices are available in the market, which can be used in conjunction with a barcode scanner or an Android-enabled device. Some options and variations in the Pick-by-Light system include:
Internet-of-Things (IoT) Pick Lights
These Pick-by-Light systems make use of industrial-grade Internet of Things (IoT) devices that are integrated into the system through wireless and cloud-based connectivity. Picklists can be initiated under a particular order picker’s name, allowing him to pick SKUs based on the pick lights indicated.
Hardware as a Service (Haas)
There are some Pick-by-Light providers who offer their services on a HaaS leasing model. This allows the warehouse to easily adjust the number of light modules they require each month, depending on changes in the inventories, SKUs, and market trends.
Pick-by-Light Carts
Other Pick-by-Light systems also make use of order picking carts that are integrated into the pick-by-light system. This allows a more efficient order picking process, whether they make use of batch picking, zone picking, or whatever picking strategies they employ in their warehouse.
Also called Light-Directed Picking systems, these innovative Pick-by-Light systems are so effective that they have been proven to increase productivity by as much as 50%. At the same time, the occurrence of picking errors have also been reduced by a high 67% when making use of this pick-by-light system.
Put-To-Light
A variation of the pick-by-light system is the Put-to-Light system, which is an innovative and efficient way to replenish stock. In this mode, the light indicators are not meant for order picking but are instead used to replenish stocks on particular boxes as accurate as possible. The system is likewise integrated into the central software and the Warehouse Management System for proper and accurate tracking of items and inventories.
Voice Directed Picking
When a large number of SKUs are being processed in a warehouse, it is simply too tedious and inefficient to make use of the standard paper-based picking list. Using a voice-directed picking system, the order picker can make use of both hands to handle SKUs or an additional RF scanner to increase the accuracy as well as the productivity of the picking process. The use of these wearable voice-directed picking devices is proven to increase the efficiency of the picking process by as much as 30 percent.
Put Wall
The Put Wall is like the Cluster Picking Strategy but makes use of light indicators. A particular customer order is assigned to one of the multiple compartments that are in the Put Wall. Using the light indicator, the operator can place the right items on the designated compartment based on the light indicators.
Augmented Reality Picking
Now, this is high tech, as order pickers get to wear wearable Augmented Reality (AR) devices that combine both vision-assisted and voice-guided picking processes, allowing operators to maximize use of their hand, resulting in a faster picking process. AR gadgets make use of smart glass with digital displays that superimpose virtual images and other digital information on top of the actual surrounding environment that the operator sees.

Advanced Picking Technology System
The Take Away
The order picking process is a very important element in the warehouse operations that affects the core operations of the warehouse itself, particularly in fulfilling the orders of customers in a fast, cost-effective, accurate, and error-free way. The use of innovative tools, as well as more optimized process flows and procedures, will result in a more efficient and more productive order picking process that will positively impact your warehouse operations, and ultimately – your bottom line.

ESL for Picking
Give your business and your industrial warehouse the upper hand it needs to stay competitive in today’s digital age with the best Electronic Shelf Labels by SOLUM. Contact us today to learn more.